F-1227 Series
Embrace Inline Automation
F-1227 Series
Embrace Inline Automation
With a speed up to
300 pcs/minute 18,000 pcs/hour
APPLICATIONS
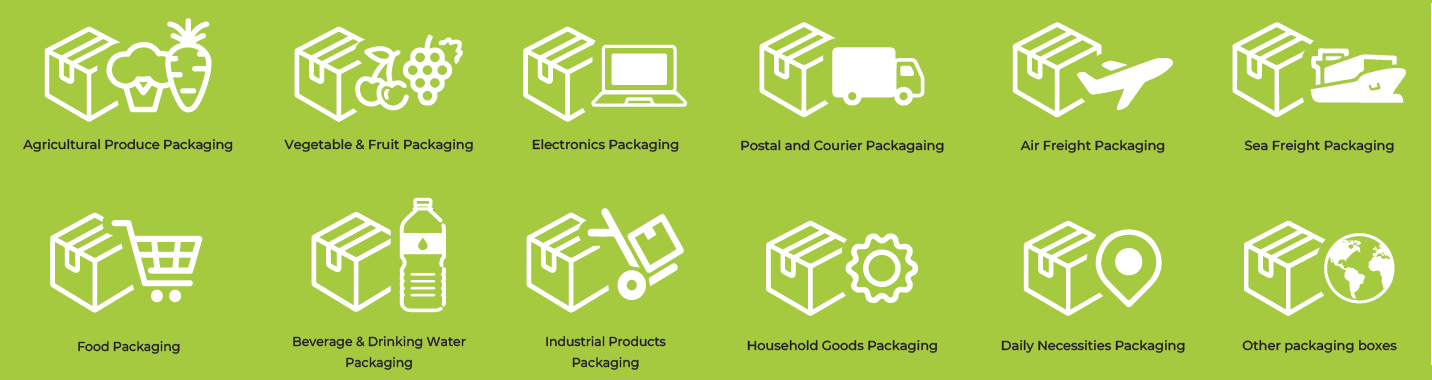
Operating System
- Production Management Software
- Remote Management System
- Ordering Set-up Function
- Intelligent Graphical User Interface
- Real-Time Information Dashboard
- Optimized Quality Management
- Downtime Information Processing
- Customized Functional Reports
-
Computer Interface Control System
Centralized control system, ensuring synchronized operation and status updates for each unit. -
Intelligent Graphical User Interface
Operator can efficiently access information and navigate seamlessly, with the flexibility to switch between various box-type production modules.
-
Ordering Set-Up Function
Adopting simple graphical user interface, the system automatically interprets the relevant functional parameters of each unit, eliminating the necessity for manual repetitive adjustments.
Feeder Unit
- Servo-driven feeding system, capable of adapting to various conditions of corrugated sheet.
- Sunrise's vacuum system enhances the flexibility tolerance of corrugated sheets, minimizing feeding challenges resulting from variations in inconsistent cardboard quality, such as titling or shifting issues.
-
Suitable for cardboard sheets with a thickness range of 1.5~9mm (AB-E flute), it accommodates to a variety of production requirements, including different thicknesses of cardboard sheets feeding.
-
Connect to the computer system for preconfiguring corrugated sheet types and dimensions, allowing for automatic adjustments in sheet feeding distance, gap between feed rolls and stopper positions.
-
Maximize stroke extensions automatically adjusted feeding mechanism to minimize damage to the cardboard sheets.
-
工-Beam Steel Structure
Minimize operational vibrations.
Ensure stability throughout the feeding process.
Improve the precision of the feeding mechanism.
-
Servo-Driven Feeding System
Servo-driven feeding system, in conjunction with Sunrise's designed vacuum system, enhances adaptability to varying qualities of cardboard sheets.
-
Semi-Cut Lead Edge Feeding Wheels
Semi-cut lead edge feeding wheels for easy and time-efficient replacements.
Printer Unit
-
The “RETURN” function with automatic restoration for precise print positioning, enhances machine efficiency and significantly reduces waste production.
- The vacuum transfer device minimizes displacement of print dots, allowing for adjustable gaps between the cardboard sheet and printing plate to achieve the state of “kiss-touch.” This ensures high print quality for both print dots and full-page printing.
- Doctor blade chamber inking device delivers a consistent ink volume during both high and low-speed rotations, guaranteeing clarity in print dots, fine text and even full-page printing.
-
Doctor blade chamber inking device offers easy maintenance, minimal ink consumption, short cleaning time and high system stability.
- Pneumatically controlled anilox ink transferring timming
- Automatic printing plate locking device
- Automatic ink shortage detection system
-
Doctor Blade Chamber Ink Distributing System (Optional)
A doctor blade chamber inking system ensures stable print quality and ink consistency in high and low-speed operations. The optional quick-change blade system allows replacement in under one minute. -
Quick-Lock Print Plate Feature (Optional)
Quick printing plate replacement system allows for tool-free disassembly and installation of plates, effectively reducing order changeover time. -
Quick Ink Washing System
User-friendly interface equipped with a one-press automated quick ink washing system to simplify the procedural workflow.
-
One Press "RETURN" Feature
Following a required pause or shutdown, simply press “RETURN” to resume production without the need for additional adjustments.
-
Automatic Ink Shortage Detection System
To protect the anilox roll from damage caused by insufficient ink, the system will activate an alarm notification upon detecting an ink shortage. -
Quick Change Blade Device
Pneumatic screws allow for blade replacement less than 1 minute, easy mainteance.
Slotter Unit
- The dual-shaft slotting mechanism with independent knife shafts enables unrestricted box height, prevents collisions, and simplifies slotting depth adjustment without the need for the tool dissassembly, effectively saving operational time.
- The linkage plate, in collaboration with linear guides and a ball screw, enhances the efficiency and precision of controlling the slotting and creasing operations for corrugated sheets.
- The slotting knife's fixed feeding gap eliminates adjustments for cardboard thickness, enhancing operational efficiency.
- Upon entering cardboard box dimensions needed, the machine automatically interprets slotting knife movement positions, simplifying operations and meeting production requirements.
- Achieving pre-creasing forced strengthened and enhanced creasing strength.
-
One-of-a-kind Slotting Mechanism
By employing a lightweight drive shaft for power transmission and ensuring the slotter moves seamlessly, the knives' lifespan has been significantly extended. -
Lateral Movement of Slotting Mechansim
The moveable plates ensure effective and precise control of slotting and creasing processes, while also reducing consumable costs related to the lateral movement of the knife holder. -
Characteristics of the Mechanism
Individually adjusting each set of mechanisms ensures optimal control performance. The structure design is compact, user-friendly, providing precise positioning, and ensuring excellent stability.
Die-Cutter Unit
- A 7-stage speed compensation system ensures precise synchronization of linear speeds between the anvil and the die-cutting cylinder.
- The quick-lock functionality of the die-cut mold (optional) enhances efficiency and decreases the time required for mold replacement.
- The electric anvil oscillation device evenly distributes the wear on the anvil surface, thereby extending the lifespan of the anvil roll.
- Trimming blade anvil grinding device
-
Electric Anvil Oscillation Device
The electric anvil oscillation device evenly distributes the wear on the anvil surface, thereby extending the lifespan of the anvil roll. -
Quick-lock Die-Cut Mold Device (Optional)
The quick-lock feature of the die-cutting mold eliminates the necessity for screw tightening, enhancing efficiency, and reducing downtime during mold replacement. -
Trimming Blade Anvil Grinding Device
Trimming blade anvil grinding device allows for quick anvil resurfacing process within 5-10 minutes.
LAYOUT
When used in conjunction with other devices, variations in dimensions and specification may occur.
SPECIFICATION
Unit:mm
Models F Fixed / S Open Closed |
F-618 Series (27.5") |
F/S-925 Series (37.5") |
S-1227 Series(50") |
S-1628 Series (66") |
S-1633 Series (66") |
F-1227 High Productivity (50") |
Production Speed (minute / hour) |
350 / 21,000 | 320 / 19,200 |
250 / 15,000 |
150 / 9,000 | 150 / 9,000 | 300 / 18,000 |
Max. Cardboard Size (Continuous Feed) |
600 x 1800 | 860 x 2500 |
1150 x 2700 |
1520 x 2800 | 1520 x 3300 | 1100 x 2700 |
Max. Cardboard Size (Skip Feed) |
N/A | 1200 x 2500 |
1600 x 2700 |
2000 x 2800 | 2000 x 2800 | 1250 x 2700 |
Min. Cardboard Size | 200 x 455 | 270 x 750 |
340 x 750 |
450 x 750 | 450 x 750 | 340 x 750 |
Max. Print Area | 600 x 1700 | 870 x 2400 |
1170 x 2600 |
1560 x 2700 | 1560 x 3200 | 1170 x 2600 |
Repeat Print Area | 700 | 953 |
1272 |
1676 | 1676 | 1272 |
Cardboard Thickness | 1.5 ~ 9 | 1.5 ~ 9 |
1.5 ~ 9 |
1.5 ~ 9 | 1.5 ~ 9 | 1.5 ~ 9 |
Max. Width of Glue Tab | 45 | 45 |
45 |
45 | 45 | 45 |
Max. Die-Cutting Area | 600 x 1400 | 900 x 2300 |
1200 x 2600 |
1600 x 2700 | 1600 x 3200 | 1200 x 2600 |
TV Top Print BV Bottom Print |
TV | TV |
TV / BV |
BV | TV / BV | TV |